Carmen thought I should spend a little more time in the shop today. I didn’t have anything in mind, but while poking around we found a chunk of cedar fencing that I had used as a test for my jointer. We had jointed it down to around 0.47″ thick, although it wasn’t particularly uniform: I hadn’t gotten my thickness planer back then, so it’s quite possible it had a fair taper in thickness, and it was by no means flat.
But it was cheap, and lying around, so I thought that it might be fun to practice making some simple boxes. The idea was to simply cut some lengths of the board to 5″, and cut rabbets 1/4″ wide and 1/4″ deep on three sides of each of the four pieces that will form the side and on all four sides of a fifth piece that will serve as the bottom. I used my (not very accurate) cross cut sled and set it with a stop block so it would cut a slot half the thickness of the board, and then adjusted the table saw so it would cut half the thickness high. I don’t have any gauge blocks, so I just used a drill bit and adjusted it so the teeth were flush with a 1/4″ drill bit. I then just “nibbled” the rabbet out with multiple passes.
It took me about fifteen minutes to cut all the rabbets on the ten pieces. I then squirted some Titebond II into the joints, and clamped it all together. The fit wasn’t amazing, but was credible and a little sanding (especially on this super soft cedar) will probably tidy it up to reasonable levels. I’ll get a picture tomorrow when its done.
Every time I do one of these projects, I try to think about how I could have done it better. I think a few sources of error are likely:
- The lumber was cheap, soft and really warped. You can’t expect micron precision from a board which has over a half inch of bow in its six foot length.
- The lumber was not sized properly. If I really cared, I’d probably joint one edge and one face, then rip the stock to a consistent with and run the stock through my thickness planer.
- The most obvious problem is that my cross-cut sled isn’t particularly square (I suspect about 1/4 degree or so, which actually adds up to around half a millimeter over a five inch span). I should try to make something better in the future.
I also am using a conventional sawblade which leaves a somewhat jagged profile, it would likely be better to use a flat bottom blade.
But in any case, a few passes with my random orbit sander will turn the box into something that I could finish with some Danish oil or poly and used to display dried flowers or hold keys or … well.. it’s a box.
Still, a very simple box, and a nice little shop project to close out 2019.
Happy New Year’s Eve, all.
Addendum: here is the box out of the clamps. It’s not amazing or anything, and because of the warping and general unevenness of the material, the joints aren’t as even or as tight as I like. But as I said before, a couple of coats of wipe on finish and it will be a useful little container for flowers or keys or whatever. It’s also pretty good practice for making drawers.
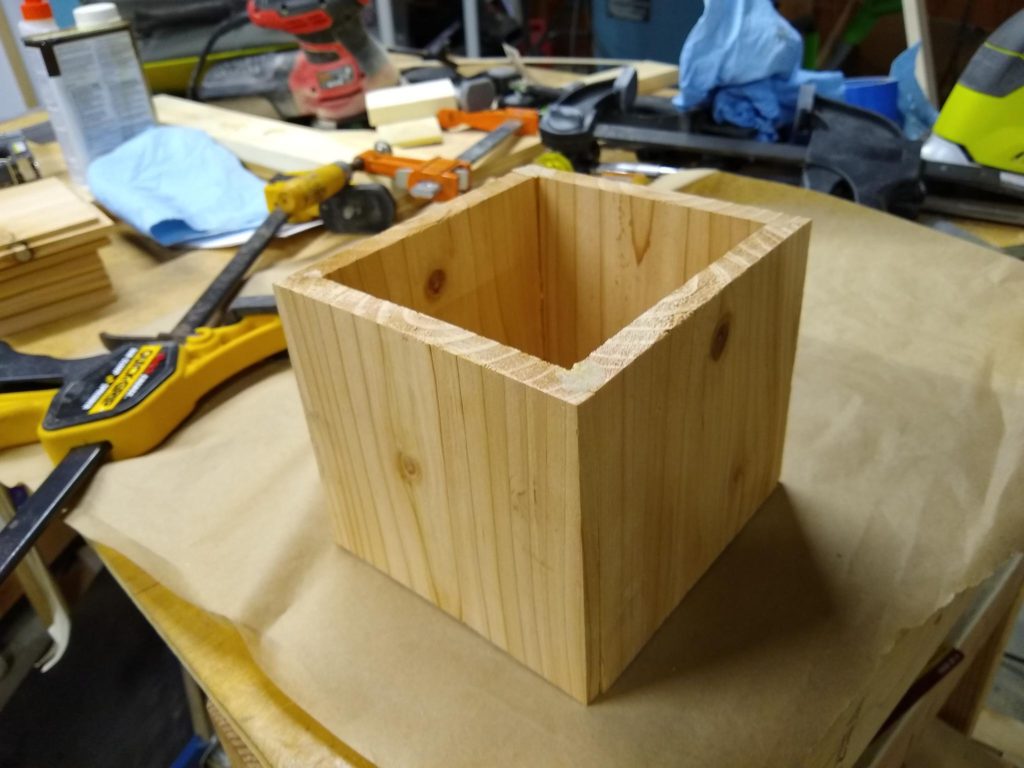
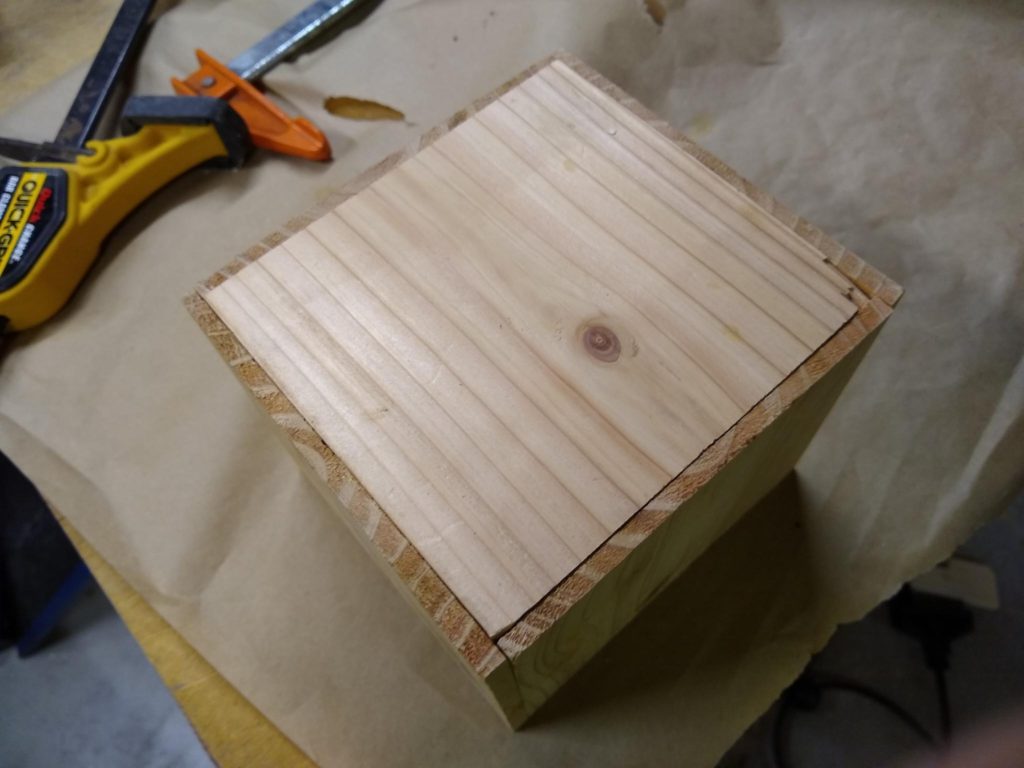
This isn’t the most amazing way to make a box. The more “proper” but still easy way would be to use a technique like this, but I don’t have a dado stack for my saw, and it would (I think) require a change in the setup to cut with a narrower blade. Still, I might give it a whirl anyway. My next bit of shop furniture will almost certainly include drawers, so I need the practice.
Addendum to the Addendum: No doubt some will complain that the way I did this was wrong: that you need a dado to hold the rabbeted bottom into the drawer, and that only using glue is a recipe for disaster. I’ll defer to more talented and experienced woodworkers than I to answer this criticism (although I must admit that I think his generalization of his small scale tests to larger scale tests is completely off base, and there is every reason to believe that the strength of a drawer bottom that is glued in place drops as the size goes up, not increases as he suggests). But in any case, the wood here is very soft and frankly weak, and this isn’t meant to hold a great deal of weight or take a beating. And, it was just a practice. When you build stuff in your workshop, you can build it to your expectations.
No comments:
Post a Comment