When looking at the performance of a vehicle, weight is one of the most important factors in the equation. Heavier vehicles take more energy to accelerate and are harder to stop. They’re also more difficult to control through the corners. Overall, anything that makes a vehicle heavier typically comes with a load of drawbacks to both performance and efficiency. You want your racecar as light as possible.
However, now and then, automakers have found reason to intentionally add large weights to vehicles. We’ll look at a couple of key examples, and discuss why this strange design decision can sometimes be just what the engineers ordered.
VIBRATION
Anyone who has taken a course on vibrations in university will know that adding mass typically changes things for the better as far as vibrations go. More mass reduces the natural frequency of a system. In a vehicle, if the natural frequency of a chassis or subsystem drops lower than that of excitations from things like the road, drivetrain vibrations, or the engine, vibrations felt throughout the vehicle can be reduced precipitously.
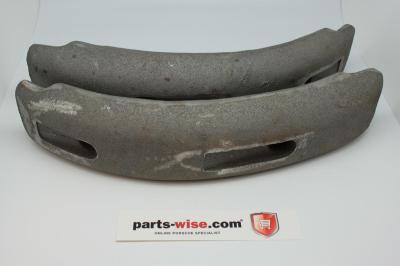
A common example is the Porsche 912E, which substituted a smooth-running six-cylinder engine for a clattery Volkswagen four-cylinder engine. When designing the vehicle to accept this engine, Porsche engineers decided to add a hefty 12-pound weight underneath the transmission cross member. The weight is listed as a “vibration damper,” and likely changes the natural frequency of the rear subframe enough such that it is below that of the vibrations generated by the engine. Adding twelve pounds of dead weight to a cheap, low-performance “sports” car has little noticeable negative effect, but can make a difference in the feeling of refinement, if less vibration is transmitted from the engine to the cabin.
Porsche aren’t the only ones to have pulled such a trick. Toyota used a bolt-on weight on certain Hilux models to reduce drivetrain vibrations, mounted to the transfer case of used to tamp down on excessive vibration. Weighing around six pounds, it was just enough to make a meaningful difference. Meanwhile, the added weight would hardly be noticed on a vehicle with a kerb weight in excess of 3480 lbs.
Volkswagen included a similar item, approximately 25 pounds, in the rear of mid-90s Golf Cabrio models. The “rear added mass” was apparently included to cut down on vibrations.
This technique is still used to this day, though often in a less obvious manner. Engineers work hard to reduce noise, vibration, and harshness in new models, known in the industry as “NVH.” Tacking on a big lump of metal a la the 912E is a quick way to deal with a vibration problem in an existing model. However, if you’re designing a car from the ground up, you can be tidier about your work. Frames and cross members can be designed with thicker cross sections, or extra material can be added to things like engine mounts or brackets to more subtly alter the picture. However, if a vehicle is nearing production and there’s no time to change the molds for other parts, sometimes a little bolt-on weight gets tacked on to tamp down on those nasty little vibrations.
Automakers sometimes go even further, however. Dodge has mounted active mass dampers that shake weights out of phase with the vibrations created by the engine in their RAM trucks. The shaking from these weights destructively interferes with the shaking of the engine, and when tuned properly, can cut down heavily on vibrations throughout the chassis of the vehicle.
Mass dampers have been used in motorsports too, with the Renault Formula 1 team pioneering the technology in 2005 before it was outlawed by the sport’s governing body. In this case, the damper consisted of a 19-pound disc that could move in a vertical plane, held in place by springs, with its movement damped by oil. The disc would help absorb energy from the car hitting bumps in much the same way as tuned mass dampers help reduce oscillations felt in skyscrapers, and was considered a significant competitive advantage for the team until it was banned from competition.
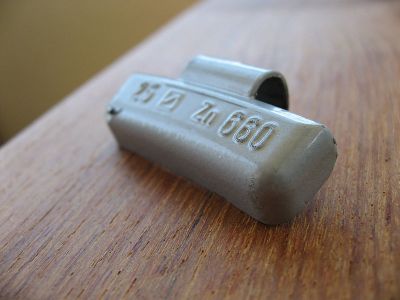
Of course, we can’t forget that one of the most common times weight is added to a vehicle is during a wheel balance. Tires and wheels aren’t always of perfectly homogenous construction, and can have heavy spots. Rotate them up to speed, and you’ll get all kinds of horrible shakes and vibrations throughout the car. However, with the aid of a balancing machine, a few weights can be stuck on to balance all that out.
BALANCE
Sometimes though, large weights are added to a vehicle to aid in balance and grip. A great example is the 1957 Willys FC-150 truck, which mounts a hefty 265 pound weight over the rear wheels. In this case, the truck as designed has the engine and passenger cab way up front on the chassis, meaning all the weight is very forward-biased. This has the rather negative effect of making the vehicle want to lift the rear wheels under hard braking, and just generally makes the vehicle unbalanced an difficult to control. The solution was obvious: chuck a big weight on the rear to keep those wheels on the ground.
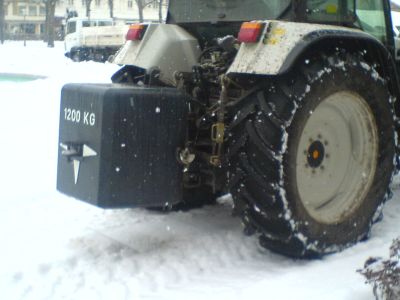
It’s a very simple solution, of course. Back in the 1950s, petty concerns like fuel economy and efficiency simply weren’t front of mind. Thus, it was easy to slap a weight on and be done with it. These days, trucks are designed with a little more finesse and are usually plenty heavy all around, so such obvious measures aren’t needed. Regardless, it’s still important for a vehicle’s weight distribution to be appropriate, whether loaded or not, to maintain good handling.
In fact, when it comes to pickup trucks, a common solution to add traction in the winter is to simply add a dummy load in the bed. A few hundred pounds of sand or pavers can help reduce fishtailing or spinning up the rear wheels in the snow. It comes at a cost to fuel economy, but if it keeps the truck out of a snowdrift, you’re saving plenty in towing fees to make up for it.
Similar measures are often used on tractors to help them pull implements and not lose grip in mushy terrain. These may be applied to frames on the front or rear of the tractor, or even directly on the wheels themselves, helping to increase the force pressing the tires into the ground for more traction. These can weigh in the thousands of pounds at the high end.
IT’S NOT ALL BAD
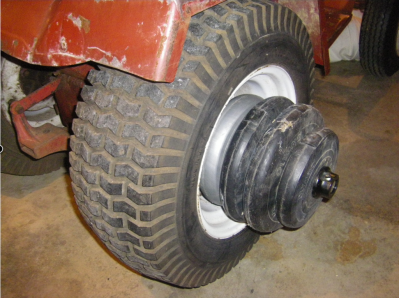
As it turns out, more weight is not always a bad thing. If a little extra weight helps cut down on annoying vibrations, or solves some tricky handling issues, it’s usually worth the trade-off. If you’re competing in motorsport, and need the ultimate in performance, cutting out every last bit of weight makes sense. However, for daily use on the road and elsewhere, often a little extra goes a long way to solving some garden-variety engineering problems!
No comments:
Post a Comment