I doubt I’m the only one who penned up plans for an “apocalypse-ready” bike build when they were ordered to stay indoors and cover all breathing holes at the start of the Coronavirus pandemic. I was afraid of the unknown, and my mind anxiously wandered to questions of resource availability and access. The ideal bike to pedal into a desolate landmine was fully rigid or fully coil-sprung, with heavy downhill casing tires, robust bits throughout, and of course, internal gearing.
Eventually I shook my head hard enough to remember that our ancestors lived through similar pandemics. My anxiety ebbed, but the question of internal gearing lingered loudly, so I did what I do. I researched. Are we banging expensive derailleurs against rocks and replacing drivetrains annually out of mere stubbornness, or is there some merit to our transmission hesitations?
In order to peel back both the yea and the nay corners of the internal gearing discussion, I contacted the engineers and business owners behind Cavalerie Bikes, Cycle Monkey, Effigear, Gates, Nicolai Bicycles, Pinion, Rohloff, Zerode Bikes, and a few custom frame builders. Their thoughts on why we don’t see more gearboxes on mountain bikes point toward several cultural factors alongside a slew of mechanical ones.
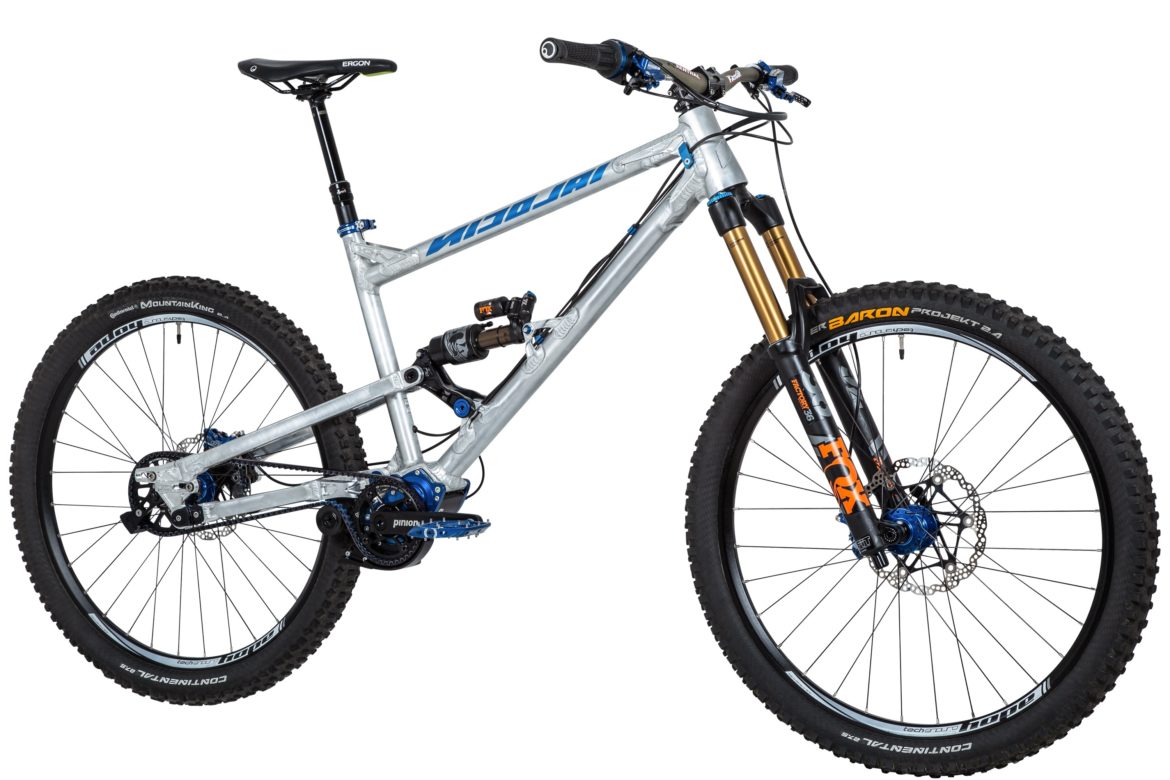
Pinion is currently leading the gearbox market, with more than 50,000 gearboxes on bikes since co-founders Christoph Lermen and Michael Schmitz met at university in 2006. Their finished product came about in 2012, and Lermen says they have since had very few issues with that original design. “Our core market is in Germany, the Dutch market, Swiss, and also the North American market with Gates as our service partner in the US. Most of the bikes are trekking or touring bikes. At the moment we also have 15-20% mountain bike customers, but certainly, 80% is trekking. Those people who are looking for a really reliable product where you don’t have to do any maintenance on the transmission.”
Advantages
The advantages of having an internal transmission on your mountain bike are many. The most popular benefit is the system’s durability and requisite longevity. External drivetrain owners who ride often might replace their chain, cables, and housing three or four times per year, and the chainring and cassette once annually. As those components wear and their precise angles begin to dull, performance suffers. The chain is pulled laterally across the cog teeth under heavy loads, and as dirt and debris are introduced the metal is essentially sanded away.
Like a sturdy single speed, all of those wear issues are diminished when the gears are wrapped in a sealed oil bath. The external components are then replaced with a tougher belt or chain that maintains a perfectly straight chainline throughout its life, and the whole system lasts far longer. Simply change the oil once a year, and you’re good to go.
That durability is increased on gearbox bikes, as the system has fewer external parts susceptible to breaking on impact. There’s no derailleur to slam into rocks, and no cable housing or pulley wheels to pack with mud. Furthermore, without a need to shift and flex, the chain and cogs can be more robust, and when an errant stick launches up into the drivetrain there’s less likelihood that the chain or belt will be damaged. Longer-lasting components make for a more sustainable bike that contributes less waste, so why don’t we all have a gearbox between our feet? We’ll get to that.
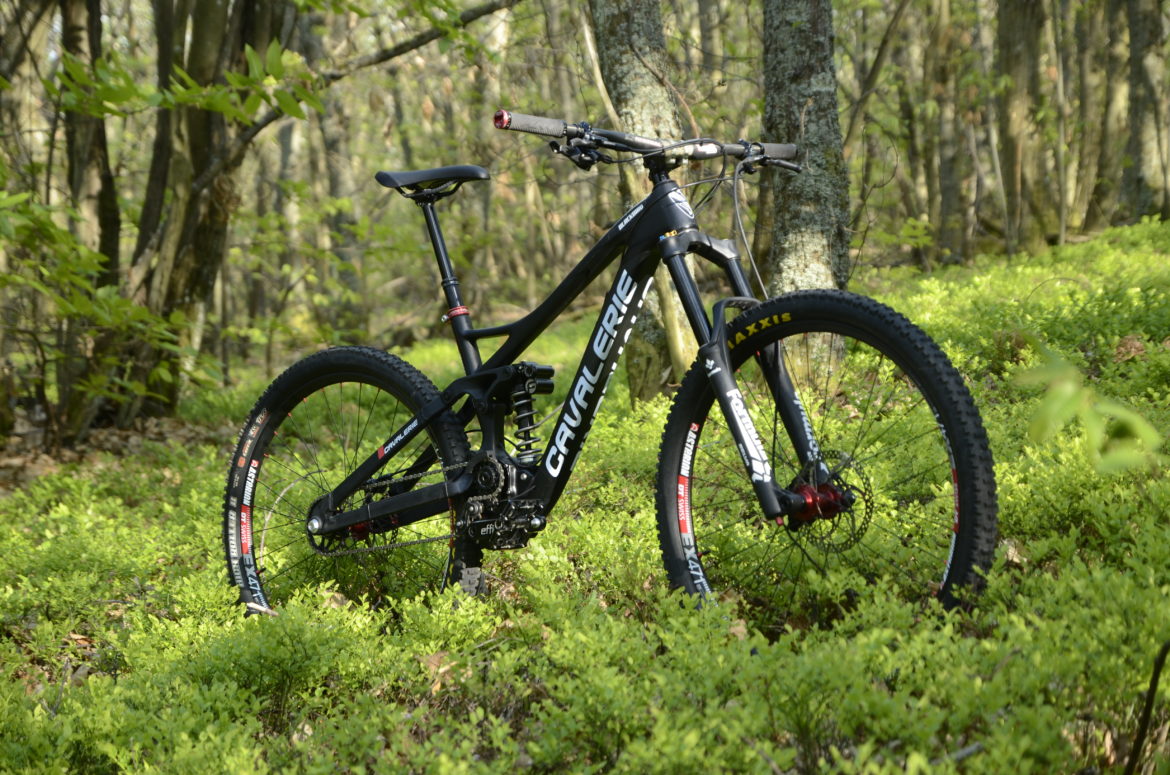
This next point fits under the compromise category. Gearboxes are located at the lowest possible point on the frame, in the center of the bike. This allows the frame to have a better balance and more planted feeling on the trail. A lot of gearbox-heads say it feels amazing in the air where both the front and rear ends weigh roughly the same. And the lighter rear wheel is also said to spin up faster with minimal weight to get rolling.
Pinion gearboxes offer a tempting option for a frame builder since the product itself is truly well-made and offers some notable benefits compared to traditional derailleur-based gears, like a very good center of gravity (almost as if riding an e-bike!), silent operation without chain slap, [the] ability to change gears while coasting, and very clean looks. Also, it is worth noting that not too many potential readily made frames exist which is the reason I decided to take the custom route.Other considerations include the use of sliding dropouts to be able to adjust chain tension like in single-speed bikes. If one is building a full-suspension frame, then a chain tensioner provided by Pinion is most likely needed. The shape and size of the bridge might also limit geometry choices since it is very hard to get enough tire clearance for a snappy-behaving chainstay length, such as 425mm or below. It can most likely be achieved by tilting the bridge and whole gearbox, but it is something good to be aware of.Custom frame builder, Jukka Mäennenä
From an industry perspective, internal gearboxes allow frame designers to create a suspension kinematic where the transmission is not affected by the drivetrain whatsoever. With a consistent chainline and cog set, engineers can better tune out many of the chain growth, pedal kickback, and braking issues that pose unavoidable compromises for derailleur-based shifting systems.
Though there are other advantages to internal gearing, the final glaring one is that riders can shift without pedaling. If you come railing into a turn and see a grunting steep climb at the exit, there’s no need to stand the bike up and clang through the cassette. You can maintain an aggressive cornering position and shift without ever moving your legs. As soon as it’s time to crack the throttle over the coming rise you’ll be in the desired gear.
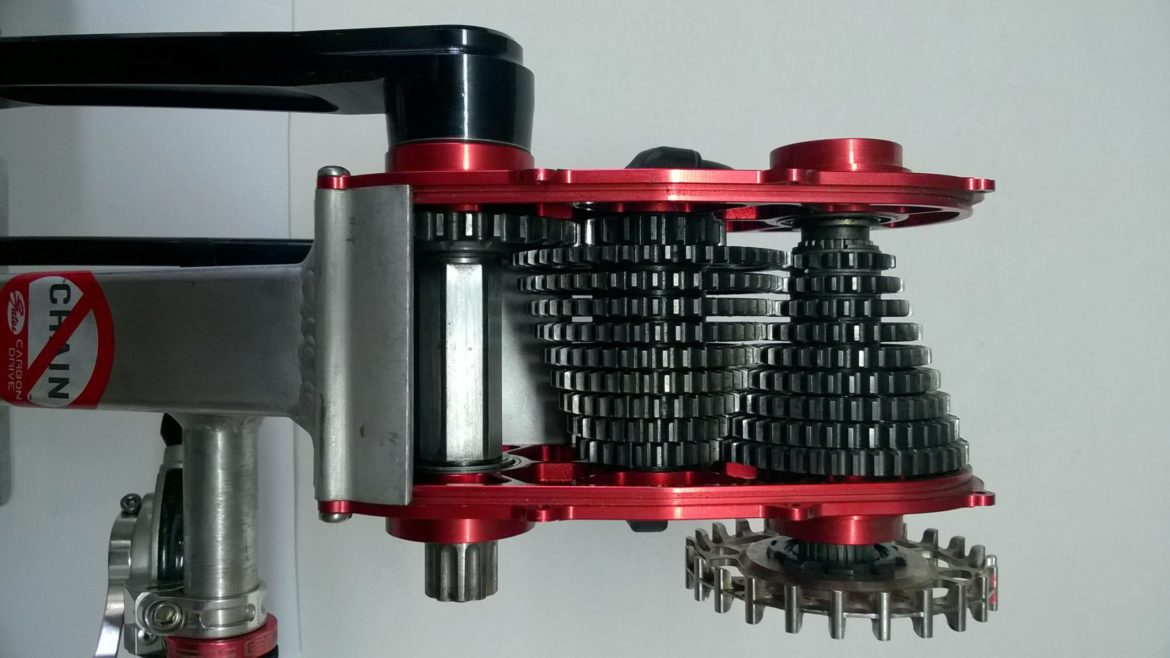
Challenges
On the flip, gearboxes add between 1.5 to 2 kilos to a bike’s total weight, depending on the external drivetrain they’re being compared to. Weight is their chief technical disadvantage, and it’s the reason you’ll only find them specced on sturdier gravity and backcountry adventure bikes. No cross country or road racer is willing to add a kilo to their nine kilo race machine in the name of durability. It would slow them down, and they don’t immediately benefit from the advantages. However, when gravity runs the show a little extra weight can be a worthwhile tradeoff for an indestructible transmission, as it is on backcountry epic rides where reliability takes precedence over everything else.
So let’s say you can lug the extra kilo around in the name of sustainability. A second perceived disadvantage of gearboxes is that the system itself creates a small amount of drag while pedaling. It’s not noticeable to most riders, but at the top of a two-hour climb the rider on a gearbox bike will have exerted a little more energy than one with a clean, well tuned, external drivetrain. According to David Roumeas from Effigear, “the added drag is around 2-4%.” The caveat here is that external derailleur systems only have that low friction advantage in dry conditions, and only if they are properly adjusted. As the chain packs with dust, and the pulley wheels, cassette, and chainring gather debris, that window of advantage narrows. Meanwhile, the gearbox bike in those same conditions continues to function as it had at the beginning of the ride.
“The playing field evens out on multi-stage events,” says Stewart Stabik, sales manager of Rohloff AG. “Things like Trans Alp and Trans Germany, Cape Epic, etc.”
After a stage, Stabik insists that there is less maintenance to be done on an internal drivetrain so riders can can put their bike away, eat, and get a massage.
Even if you are committed to precise shifting no matter the conditions, and it’s worth eating less pizza to even out that kilo of added gearbox weight, snother hiccup to consider is that, depending on the gearbox you go with, you may not be able to change gears while pedaling hard. Pinion gearboxes will not shift gears under load, and Effigear transmissions will shift into a harder gear under max pedaling pressure — but for an easier gear you’ll need to pause a few milliseconds. It’s common to shift into an easier gear while grinding up a steep pitch and on technical trails dropping the power means dropping a foot.
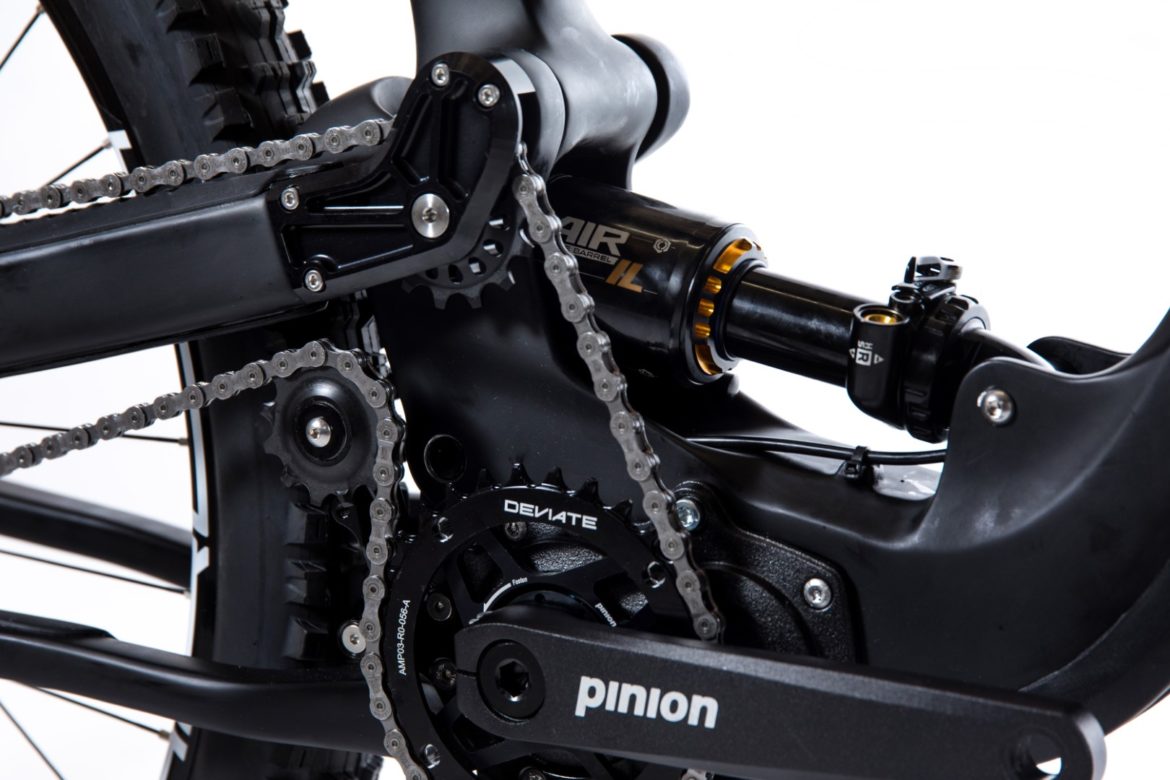
With a Pinion system, a shift can happen after your leg muscles ease off a certain amount of pressure. You can make the shift whenever you like, but the gears will not change until you let up on the gas a little. There’s no way to cram through the cogs and destroy them with poorly-timed shifts. Many gearbox users say this is easy to adjust to, and they simply shift in the natural dead spot in their pedal stroke. Dedicated derailleur veterans often run into their main gearbox peeve with this specific characteristic. Unfortunately, habits that make their way into our muscle memory can be resistant even to the most minute changes.
Neil from US-based Cyclemonkey owns a number of gearbox bikes, and offered a thorough comparison of how two of the different systems shift while pedaling.
The Pinion gearbox will be increasingly difficult to shift in either direction as the torque going into the gearbox increases. This presents itself most commonly when trying to shift into an easier gear during a climb where cadence is falling and the rider starts pushing on the pedals harder to maintain forward progress, thus ramping up torque. It is rare to run into this situation when shifting into a harder gear though the principal is the same. In many cases, you can muscle the shifter to make the shift go through (though this is not intuitive to a new user who has been trained not to power shift their drivetrain). You can simulate the variation in required shifting effort when standing beside the bike and putting varying pressure on a pedal. When you try to turn the shifter, you’ll notice the difference in the effort required to be able to turn it.Effigear will shift into a harder gear under full load but will not shift to an easier gear unless torque is completely removed from the system. This is because its pawls can operate independently. Each set of pawls has a spring that pushes the pawl up to engage with the gear they sit inside of when the shifting cam is underneath the pawl set but there is no mechanism to pull the pawl back down to disengage from the gear. The gear needs to spin over the pawl to push it back into the retracted position. If the cam is still in place — the engaged gear is still selected — the springs under the pawls compress against the cam when coasting, then push the pawl back against the gear teeth just [like] the ratchet in a rear hub. If the cam has moved — different gear selected — the pawls will stay retracted once the gear spins over them and pushes them down.When changing gears while pedaling (no coasting during the shift), you end up with two gears engaged simultaneously — the one you have been using and the one you want to use next. The gear that makes the gearbox spin faster determines the actual gear ratio, which is the harder gear. So, when changing to an easier gear, the previous (harder) gear is still dominant and will not let go until there is a coasting event, which in practice means an awkward momentary interruption of the pedal stroke when trying to shift while climbing. When changing to a harder gear, you still get two gears engaged simultaneously, but in this case, you want the harder dominant gear, so you get the gear change immediately. This [Effigear] is the fastest shifting system I have ever used in the direction of a harder gear.Rohloff and Pinion use a camshaft to change gears that is designed such that the pawls always move in unison (can’t have two gears engaged simultaneously), so in order to lift a pawl to get a new gear engaged, the pawl for the previous gear must retract to allow the camshaft to rotate. The pawls are shaped such that the camshaft can push against them to directly retract them, which is why you end up “fighting” against the loaded shift.
Alongside those shifting nuances, Pinion and Rohloff transmissions can only be shifted with a twist or “grip shift,” where the Effigear system uses a more traditional “trigger shifter” lever to change gears. If you’ve ever used a grip shifter, you may know the few issues they pose. The primary problem for trail applications is that it’s easy to accidentally shift in rough sections of trail where you’re gripping the bars tightly. With these systems you can shift through multiple gears at once without pedaling, so riders might not even know they dumped through the gears until they need to pedal again. Each one of the companies I spoke with is working on a better, and likely electric, lever mechanism.
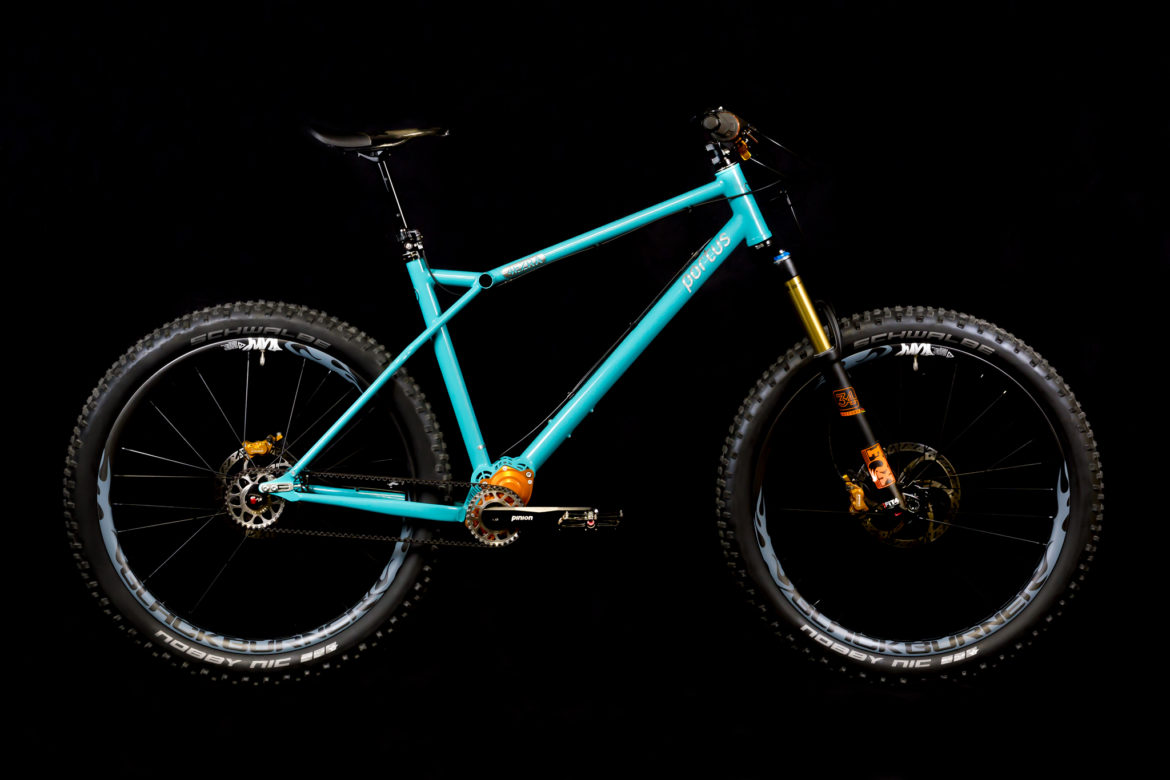
I want gearbox tech to be the wave of the future as much as the next sustainability-focused bike nerd, but there is one additional hitch. At the moment, not all gearboxes are compatible. An Effigear transmission won’t bolt up to a frame that was built for a Pinion system, and vice versa. For frame designers, that means hitching their wagon to one transmission brand, and any issues that may arise with that system. If there’s a production error or an issue getting parts to build up their bikes, the frame company is at the mercy of the gearbox company, whereas with more universal parts like derailleurs they can simply switch to another brand or model. This is an issue that will work itself out as more companies jump in the game and gearbox manufacturers determine industry standards to follow. Effigear is currently in the process of redesigning its gearbox to fit the same space and bolt pattern that Pinion uses, and they hope to have the new models available shortly.
Given the current standards and popularity of gearboxes, if something breaks while you’re on an adventure deep in the mountains, it will be rather difficult to find replacement parts. Though all of the brands currently making internally-geared hubs and gearboxes confidently offer more than double the warranty for their components compared to any derailleur system, availability remains an issue. Some of the small components can be replaced in a home shop, but a good portion of repairs to any gearbox system require the help of a trained mechanic, or that the owner ship their gearbox back to the company. As above, this issue will fade as gearboxes gain popularity and more shops start to carry spare parts.
After all of those ups and downs, where are gearbox drivetrains headed? We asked the folks at Pinion, Rohloff, and Gates where their main customer base lies, and at the moment it’s largely not in the dirt. Commuters who want a bike that they never have to maintain as well as a variety of cargo-bike solutions are a central focus for the brands. These internal gearing and belt drive manufacturers are seeing some business in the touring and adventure cycling crowd since both require robust shifting systems riders can depend on. Another potential growth area for internal drivetrains is with e-bikes, where the weight is carried by the already-girthsome motor and battery. A final, albeit smaller, slice of their profit pie is with custom frame builders who can design their bikes around gearboxes to offer clients another option for their dream bike.
With e-bikes, everyone’s wanting more powerful motors. It’s almost like a hot rod culture. The bigger motor the better. Traditional derailleur systems simply can’t handle that torque. E-bikes are designed to give additional power and support when the cranks are vertical because you can get the least amount of human power into the system, so they compensate that through their software. So there’s never a point where the force really dips naturally to ease a shift. That becomes very problematic for certain gear systems out there. They wear extremely fast. The Rohloff just happens to have a very robust internal component. So, without making any internal changes to the Speedhub since it’s introduction some 20 years ago, the product suits modern e-bikes.Stewart Stabik, Rohloff AG
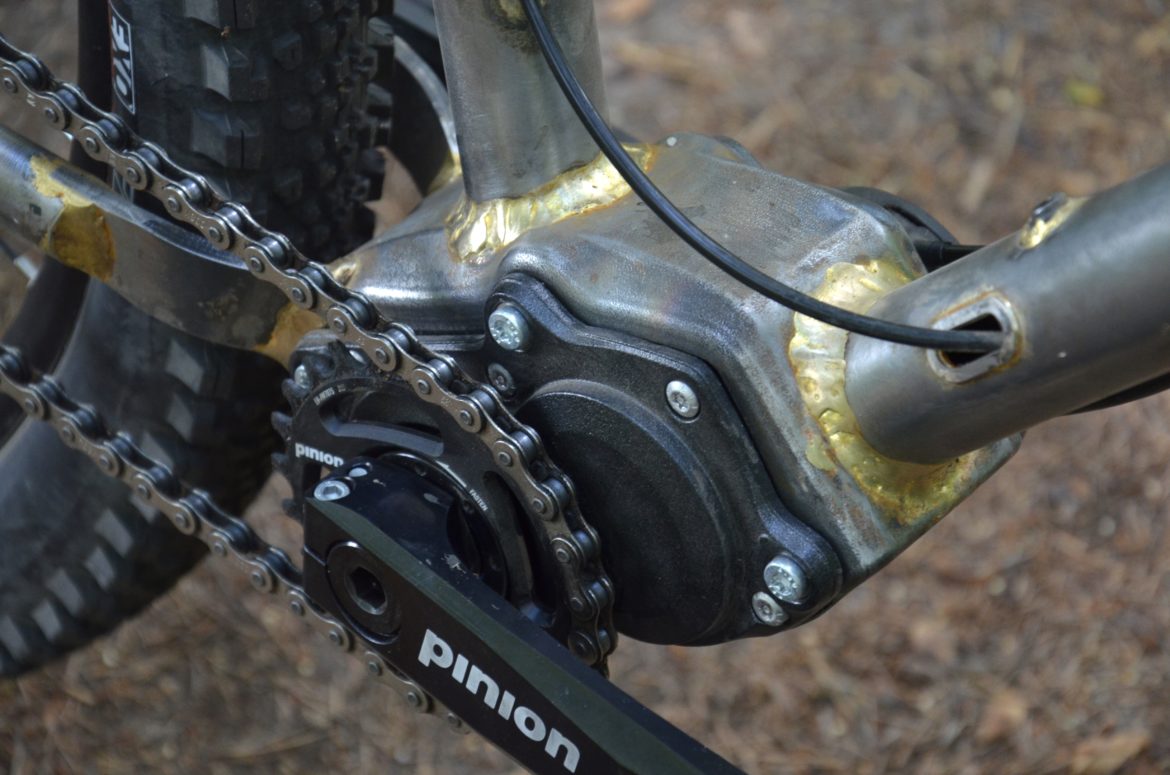
In addition to all of the benefits and drawbacks outlined above, an important factor in riders’ resistance to the everlasting gearbox is linked to our cultural identity and resistance to change more broadly. Every one of the engineers and business owners I chatted with stated their own version of the following sentiment: “the mountain bike industry is driven by trends.” Several of them spoke those words verbatim. The drivetrain solution we already have works very well, there are affordable options and blingy bits, and complaints around durability are often overlooked in the name of replaceability. Is there truth to the “trend-driven” theory? A good number of riders like to own what’s cool, what we already understand, and what friends will think looks sick when we show up at the trailhead. Will that ever be a gearbox?
The final point is embedded in the phrase “what we already understand.” When gearbox frame companies like Zerode throw demo parties, it’s folks who are new to mountain biking who come back immediately stoked on the bikes. Veteran derailleur-shifting riders are often perturbed by the nuances of the shifting system, and it can take a few rides to feel at home with the gearbox. With only one test run, a lot of those lifelong shredders don’t get a chance to find out if they can adapt.
Karl Nicolai, owner of Nicolai bikes, is currently working on an internal shifting system that will function identically to a derailleur-based drivetrain, should be almost as lightweight, and will provide most of the same benefits of a gearbox system. Best of all, the guts will be made up of parts you can find anywhere instead of proprietary transmission components. Asked about similar systems, Nicolai mentioned “the only similar system available in the past was the Honda. There are a lot of patents out there but not so many products. I’m very curious what’s coming up beside us in the coming years.” Greg Minnaar raced World Cup downhill for the Team G Cross Honda squad from 2004-2007. If you didn’t see the Honda system on their DH bikes years ago, it consisted of a cassette and derailleur inside a sealed gearbox, offering 90% of the same benefits of the current gearbox systems, with fewer drawbacks. We’ll keep you posted on Nicolai’s progress with this hot new box, which he’s been working on for over two years now.
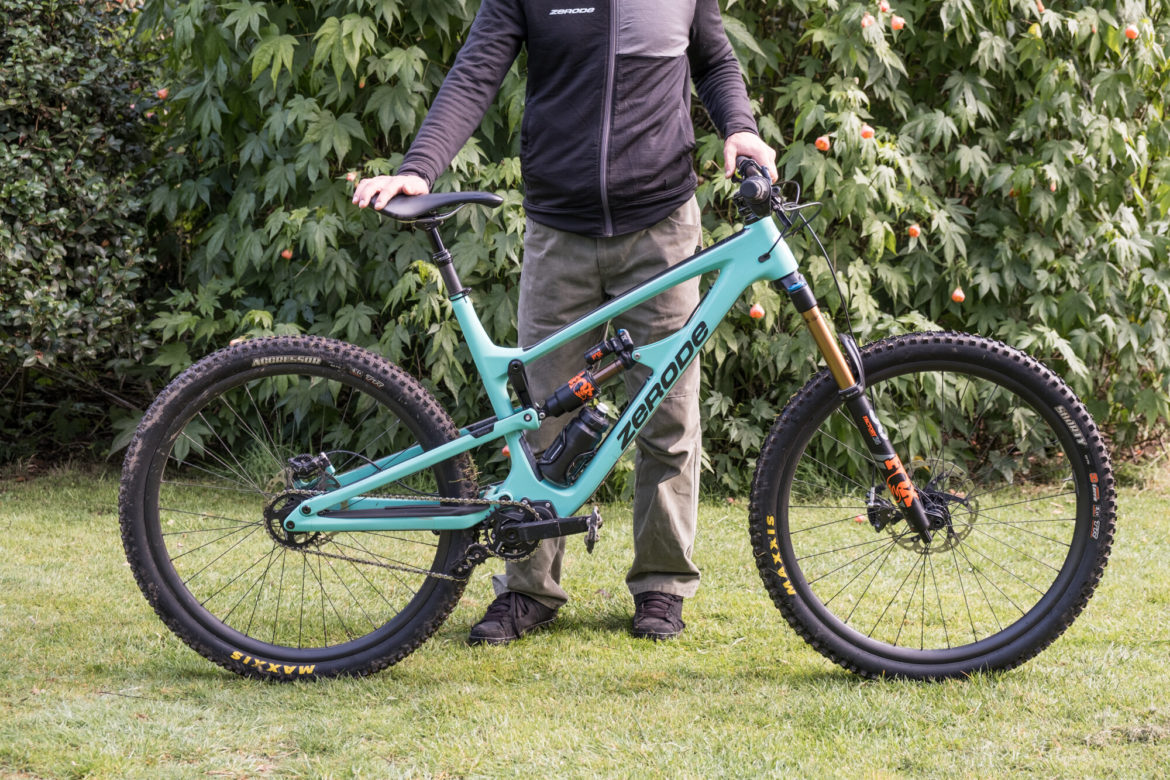
In summation
Since we mountain bikers are not jumping on the gearbox bandwagon in droves, redetermining what’s cool and funding it, these companies are focusing on different genres of the cycling industry. They’re also all working to make their systems lighter and more universally compatible while developing cool elements like electric shifting and trigger-shifter compatibility. Hopefully one of these innovations will bring more sustainable shifting systems to the fore.
I aim to ride and review a few different geabox bikes over the summer to find out just how tricky it really is to switch between transmission systems. Are there any specific bikes you would like to see reviewed on the site?
No comments:
Post a Comment