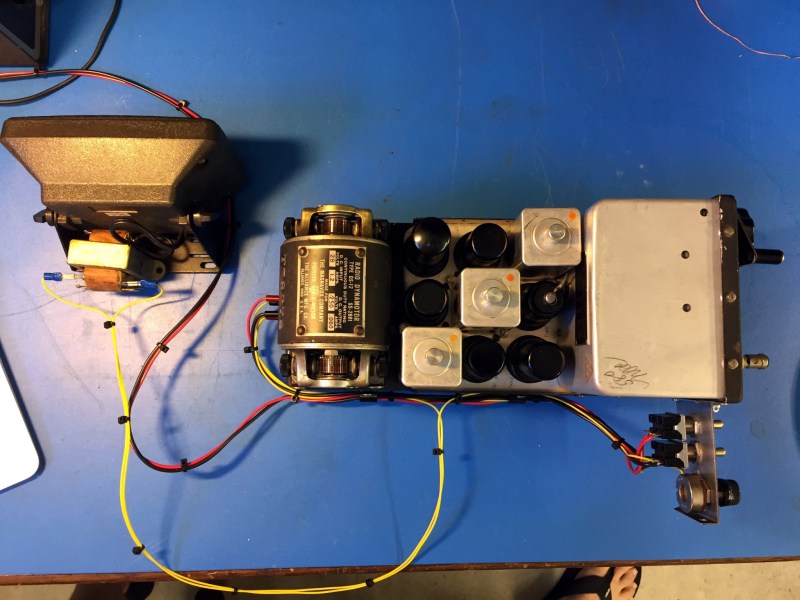
I’ve been told all my life about old-timey Army/Navy surplus stores where you could buy buckets of FT-243 crystals, radio gear, gas masks, and even a Jeep boxed-up in a big wooden crate. Sadly this is no longer the case. Today surplus stores only have contemporary Chinese-made boots, camping gear, and flashlights. They are bitterly disappointing except for one surplus store that I found while on vacation in the Adirondacks: Patriot of Lake George.
There I found a unicorn of historical significance; an un-modified-since-WW2 surplus CBY-46104 receiver with dynamotor. The date of manufacture was early-war, February 1942. This thing was preserved as good as the day it was removed from its F4F Hellcat. No ham has ever laid a soldering iron or a drill bit to it. Could this unit have seen some action in the south Pacific? Imagine the stories it could tell!
My unconventional restoration of this radio followed strict rules so as to minimize the evidence of repair both inside and out yet make this radio perform again as though it came fresh off the assembly line. Let’s see how I did.
A FLAVOR OF RADIO FOR EVERY NEED
The list of radio systems installed into WW2 aircraft goes on and on, even more so for special aircraft like night fighters which depended entirely on radio navigation and radar systems to fly their missions and jamming aircraft who’s purpose was to hide fleets of bombing aircraft or invasions of coastal territories. There were different systems for each specialized task:
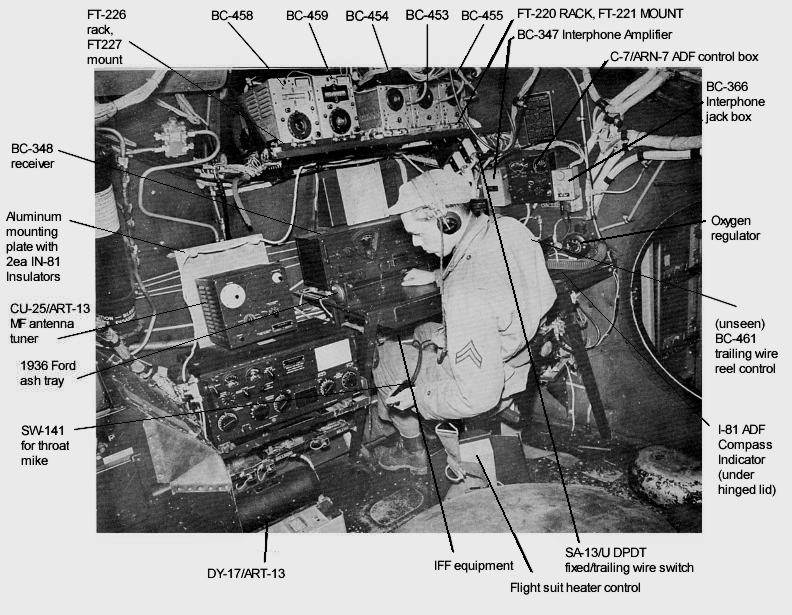
- Long range radio systems to communicate back to base, typically consisting of an ART-13 transmitter and a BC-348 receiver.
- Short-range radio systems designed for aircraft-to-aircraft communication, known as command sets subdivided into a multitude of bands.
- Air to ground radio communication equipment.
- Radar beacons to identify the aircraft as a friendly (identify friend or foe, or IFF).
- Radio navigation receivers of various types from
- radio direction finders,
- glide slope receivers for landing purposes, and
- TDOA radio navigation systems akin to modern GPS (except that you had to manually measure the time difference of arrival with an oscilloscope and line it up on special charts), such as GEE.
- Radar systems of various types.
- Electronic warfare receivers to detect enemy radar signals.
PART OF THE ARC-5 RADIO EQUIPMENT
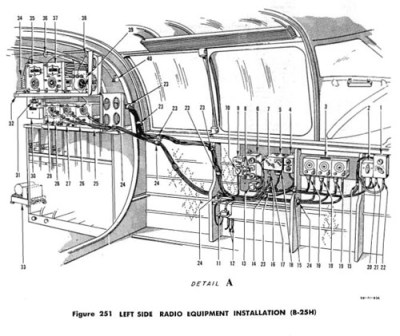
Somewhere in this menagerie of radio systems, you would find a CBY-46104 receiver. This receiver is part of a series of radio gear known as ARC-5 command sets, which describes an entire class of WW2 transmitting and receiving equipment for aircraft-to-aircraft communication. This class of equipment includes separate transmitters and receivers that can be controlled remotely by the pilots through a remote control head mounted somewhere in the flight deck.
These radios were designed in the mid 1930’s. Transmitters utilize a MOPA (Master Oscillator Power Amplifier) architecture supporting AM phone and CW (aka Morse code) transmission. Receivers use a single-conversion heterodyne architecture similar to that of big wood console radios of the era. Octal tubes were used as the active devices and the operational frequencies did not exceed 20 MHz, which was considered a high frequency for the mid 1930’s.
This radio gear was light-weight for WW2 standards, the CBY-46104 weighs only 6 lbs and is made entirely from aluminum. It is a carefully balanced chassis/radio design for weight minimization (these were installed in aircraft after all) while also remaining rugged and able to provide stable operation across MIL-SPEC temperature ranges and intense vibration.
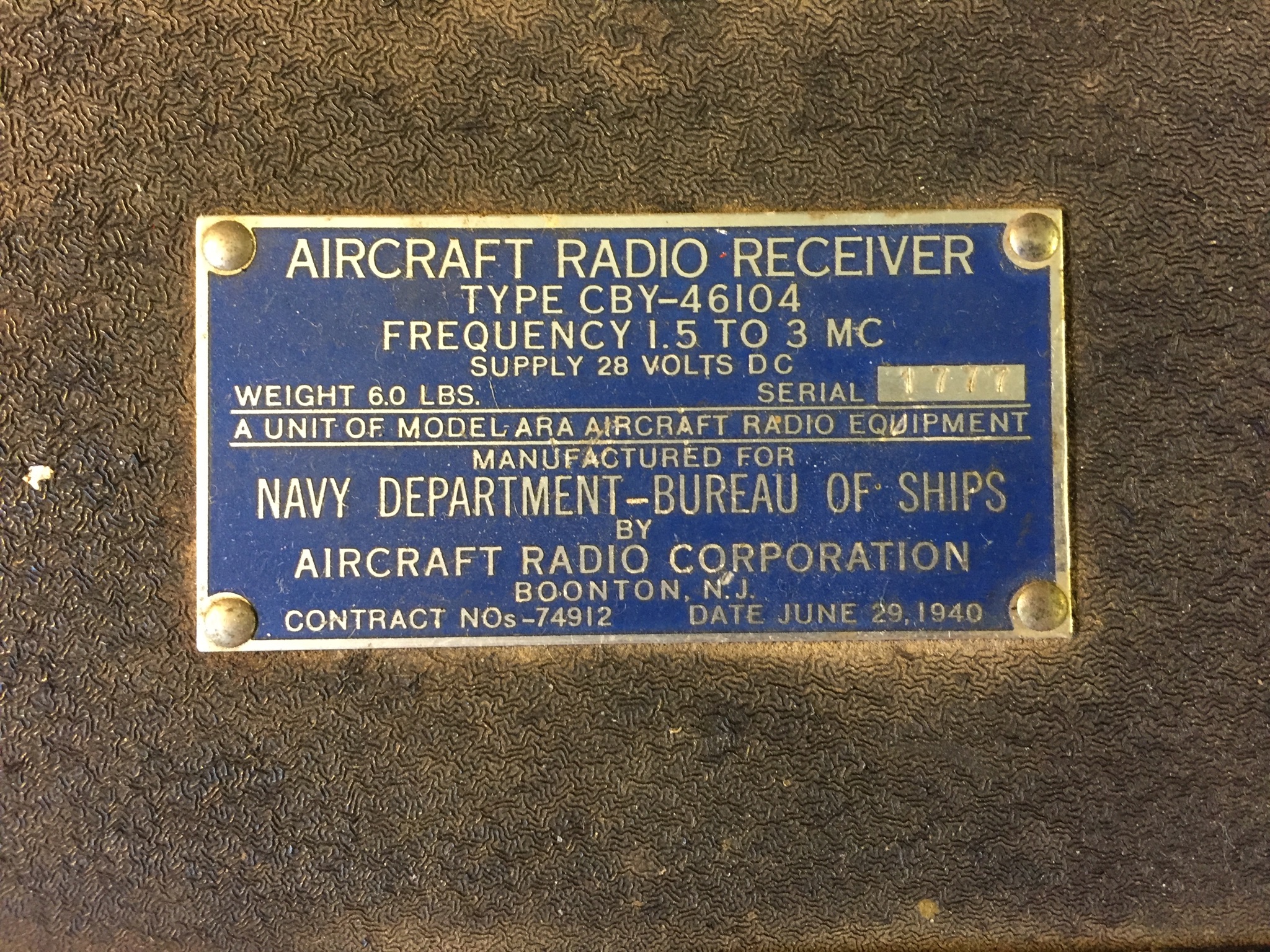
The CBY-46104 covers 1.5-3 Mc either AM or CW (it can also tune in SSB in CW mode), made by the Aircraft Radio Corporation of Boonton N.J. in February 1942 with SN# 1777. The contract for this run was #74812 dated June 29, 1940, demonstrating the ramp-up in war materiel purchasing/production in advance of Pearl Harbor. In other words, they were planning ahead for this conflict (an interesting book on this topic, how war production in the US was set up in advance by an executive from General Motors who established GM’s global supply chain in the 20’s and 30’s).
RULES OF ENGAGEMENT FOR THE RESTORATION
To preserve this historic treasure my rules of restoration were:
- No replacement of any components whatsoever.
- If a capacitor failed, then it must be re-stuffed.
- Unit must be made fully operational to original specification.
- Unit must run off of its dynamotor, as it was intended.
- No holes can be drilled, either on the chassis or on the plug-in.
- Rear power connector must stay as-is.
- No chassis modifications whatsoever.
These were not easy rules to follow because, as we know, the first step to antique radio restoration is to replace all of the paper and electrolytic capacitors, saving a lot of headache and time.
INITIAL ASSESSMENT
Instead of replacing the caps I opted to do a cursory check of the caps and try powering the unit up for an assessment. I tested the electrolytic and paper caps with a Fluke DVM in resistance mode for obvious shorts or low impedance. All caps were open-circuit as far as my DVM was concerned (unfortunately DVM’s are not sensitive enough for a proper leakage test, more on this later).
Next I had to locate documentation. Fortunately, it is easy to find documentation for WW2 radio gear because it was ubiquitous in the late 40’s through the early 70’s in amateur radio stations across the world (here is a PDF link to the manual for all or most ARC-5 gear). A typical practice of the post-WW2 era was for the Elmer hams to gift an ARC-5 receiver to a young ham working to earn their license. With such a receiver the young ham would be able to tune in radio traffic from all over the world and practice listening to Morse code (CW) transmissions.
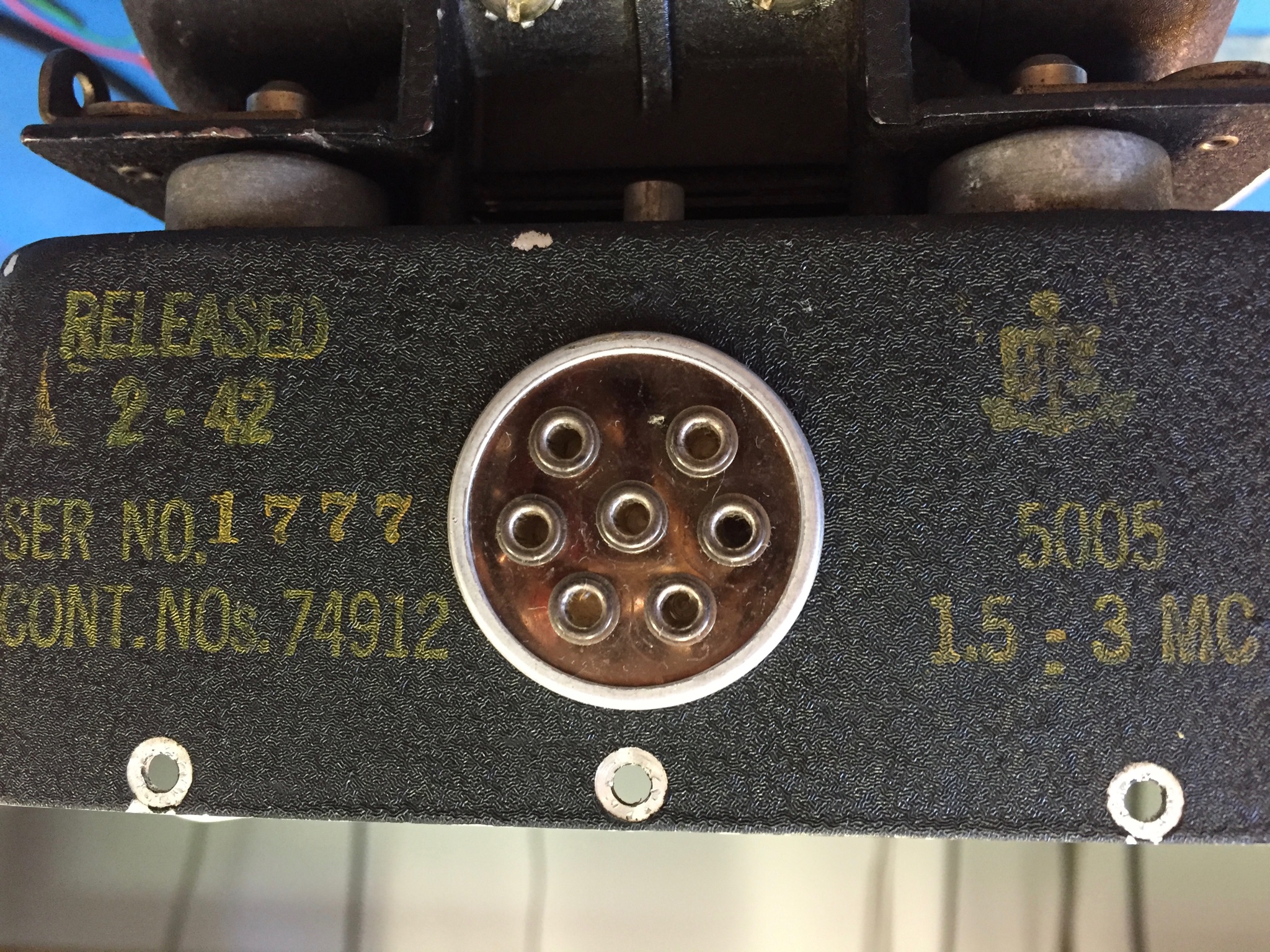
It is not easy hooking-up military surplus radios because they typically use multi-pin multi-use connectors for power and other controls. From the documentation I figured out what had to plug into the multi-pin connector on the back; +28 VDC, an external CW/AM toggle switch, RF gain control pot, 600 ohm speaker (I used an 8 ohm speaker and impedance matching transformer).
But one might ask, “with 28VDC input, how do we get high voltage for the vacuum tube plates?” Here is how they did it in WW2: This unit has what is known as a Dynamotor. High voltage was generated from the Dynamotor. Everything from receivers to transmitters that ran on low voltage DC busses used dynamotors to generate the 200-1000V, or more, needed for operation.
Dynamotors are motor-generators; in my case one end is a spinning motor at 28VDC motor and the other end is a 250VDC generator. Rather than having two motors with two shafts tied together (larger units on ships actually used such configurations) this motor is built into one compact unit with two armatures and two sets of brushes. 28VDC in, 250VDC out all the while spinning like a whirly-bird.
I removed the bells (end caps) from both sides of the motor. I applied 28V and, carefully with my finger, pushed the armature on the 28V side of the dynamotor to coax it into operation. It spun up like a 1950’s jet engine! Whrrrrrrrrrrr…..
After about 30 seconds the Whrrr sounded slightly bogged down, loaded down actually, by the vacuum tubes warming up and drawing current from the 250VDC output of the dynamotor. Then noise came out of the speaker. I hooked up my 20m dipole and to my amazement I was tuning in AM broadcast stations at around 1500 Kc. There was a lot of noise coming through the speaker likely due to failed decoupling caps that would otherwise quiet the dynamotor’s hum. The receiver was not too sensitive, and tuning was jammed up at the higher frequency ranges on the dial. It was at this point that I shut it down, this radio wanted to work and all I had to do now was clean her up and fix a few things.
SERVICING CAPACITORS AND RESISTORS
First order of business was to accurately test the capacitors because it was obvious that some were not functioning to spec. It is tough to test capacitors correctly, it requires multiple tests to troubleshoot for bad capacitors:
- Test with a DVM in ohm setting.
- Testing capacitors with a DVM in resistance mode will show which are short-circuited but it will not reveal the leaking capacitors that are only leaking ever so slightly (e.g. have extremely high DC impedance) at high voltages. DVM testing only reveals the short-circuited caps, this is a necessary first step.
- Test for specified value.
- A capacitor must operate to its specified value so it is good to test to see if the cap is functioning as a cap. This test will show if a cap is functioning as a cap and as specified. Unfortunately some leaky capacitors will measure to their specified value, so this test is not definitive.
- Electrostatic Resistance (ESR).
- In modern low-voltage electronics the key metric to capacitor goodness is ESR. This test will confirm that a capacitor is presenting a low impedance to a high frequency signal. In other words, how much series DC resistance does a capacitor present when it is measured at a relatively high frequency. Ideally, capacitors should present no resistance whatsoever, but practical capacitors do present some low resistance and bad capacitors present a lot more than some resistance.
- With that said, ESR testing is useful for testing the electrolytic power supply capacitors in tube equipment.
- Leakage.
- For high voltage capacitors, the key metric of goodness is leakage. How much current leaks through an old capacitor? If small amounts of current (on the order of single-digit uA) leak through then that capacitor is bad. A leaky cap will act like a high value resistor, in the many-multi-mega ohm range thereby reverse-biasing the grids of tubes or discharging itself causing it to not function like a capacitor at all. Leakage testing is absolutely critical and must be done for each and every cap.
Given all of that, the keys to troubleshooting tube equipment are to test the capacitance of each cap to verify that it is functioning and test the leakage to make sure it is not leaking current between circuits.
To check for value and leakage with one test device you must resurrect an old piece of test gear known as the capacitor checker. I found mine at the Dayton Hamvention many years ago for $10. It consists of a few dials and a very sensitive ‘Magic Eye’ tube which will deflect leakage is detected. Mr Carlson’s Lab has a great video on how to use one.
To check each cap I had to remove each of them from circuit, one at a time. There’s no getting around this, otherwise you might miss-read the cap value or leakage test. Remarkably enough, the vast majority of these Feb 1942 capacitors tested good. This is a testament to not replacing all the caps if you don’t have to. I found that all but three of the metal-can-sealed wax and paper caps (special to ARC-5 and other WW2 radio equipment, otherwise known as ‘flower pot’ capacitors due to the shape of their metal cans) and the electrolytic caps needed to be replaced. I opted to re-stuff the defective caps by opening the metal cans, extracting the guts, and putting in a modern replacement, then gluing the cans back together.
Resistor Care
Next I checked all of the resistors with my Fluke DVM. The nice thing about tube gear is that when the power is turned off the tubes present an open-circuit and therefore you can test resistors reliably in-circuit without removing them.
Old resistors tend to increase in value over time. Particularly the higher valued ones in the 100’s of K or M ohm range. For this radio not one resistor was out of tolerance! Amazing for resistors built before February of ’42.
SERVICING THE DYNAMOTOR
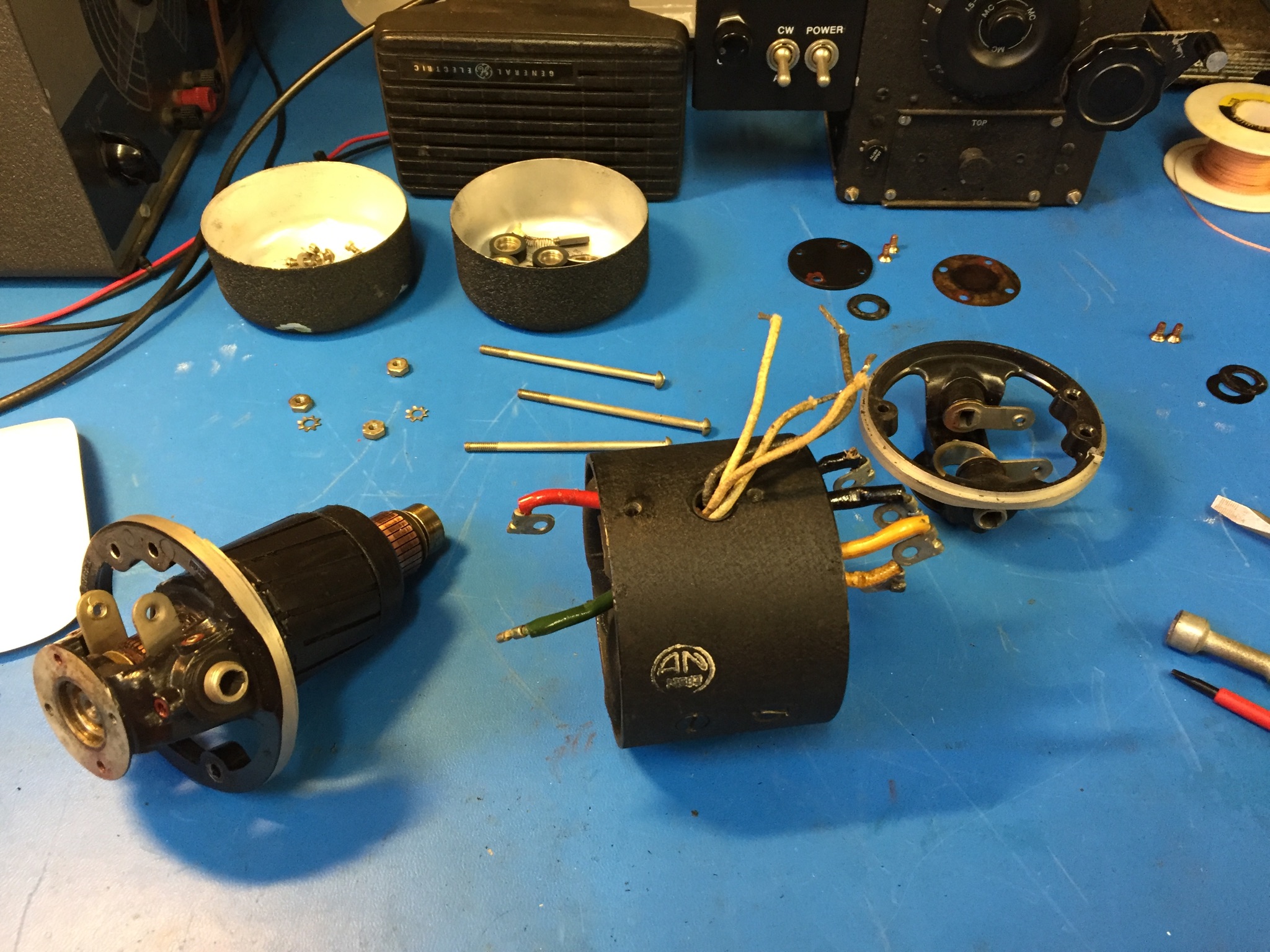
I then moved onto cleaning the Dynamotor. It was running but not well. Fortunately these are easy to service, they are designed so that anyone with a flat-head screwdriver can fix them. I found a video on servicing a similar motor and proceeded to strip mine down, clean out the old grease in the bearings, put new grease into the bearings, clean the armatures, and re-assemble. Dynamotor worked perfectly, just like new again!
PROBLEMS WITH THE TUNING VARIABLE CAPACITOR
With good resistors, good caps, a working dynamotor I then moved onto the tuning mechanism. Something was not right with it, the plates on the large variable tuning cap were literally grinding against each other. I made the necessary repairs; it appears that this unit was dropped at some point and the fixed plates, which were normally electrically isolated from ground, had popped off of their plastic insulators. I put them back into place and the tuning unit was good as new.
Old radios are like old cars, they could use an alignment from time to time. Given the changes to the tuning unit I realized that I had to do a full alignment. I followed the instructions from the original service manual, aligning the IF first (using a modern synthesized signal generator to get it spot-on), then the front-end variable cap assembly that I had just repaired. The later was tricky, with some high, medium, and low-band-specific alignments required.
With the receiver aligned I tested its sensitivity. I measured <1 uV on AM at 2 MHz, more than good enough for me and easily exceeding the original factory spec.
BUILD A WIRING HARNESS
At this point I had two toggle switches and a pot with a mess of wire shoved into the rear panel connector pins. To organize this mess and to make a more permanent functional display for the radio I built up a small external switch panel and drilled a hole pattern in it so it would simply bolt to the side of the radio using two of the existing machine screws on the case. I left the original rear power plug in place and found out that ‘miniature banana’ plugs fit perfectly into the WW2 socketed pins. I used these banana plugs to connect up the control panel and a 600 ohms speaker. With all of this I made a neat wire harness to tie it all together.
FINAL TESTING, IT’S ALIVE!
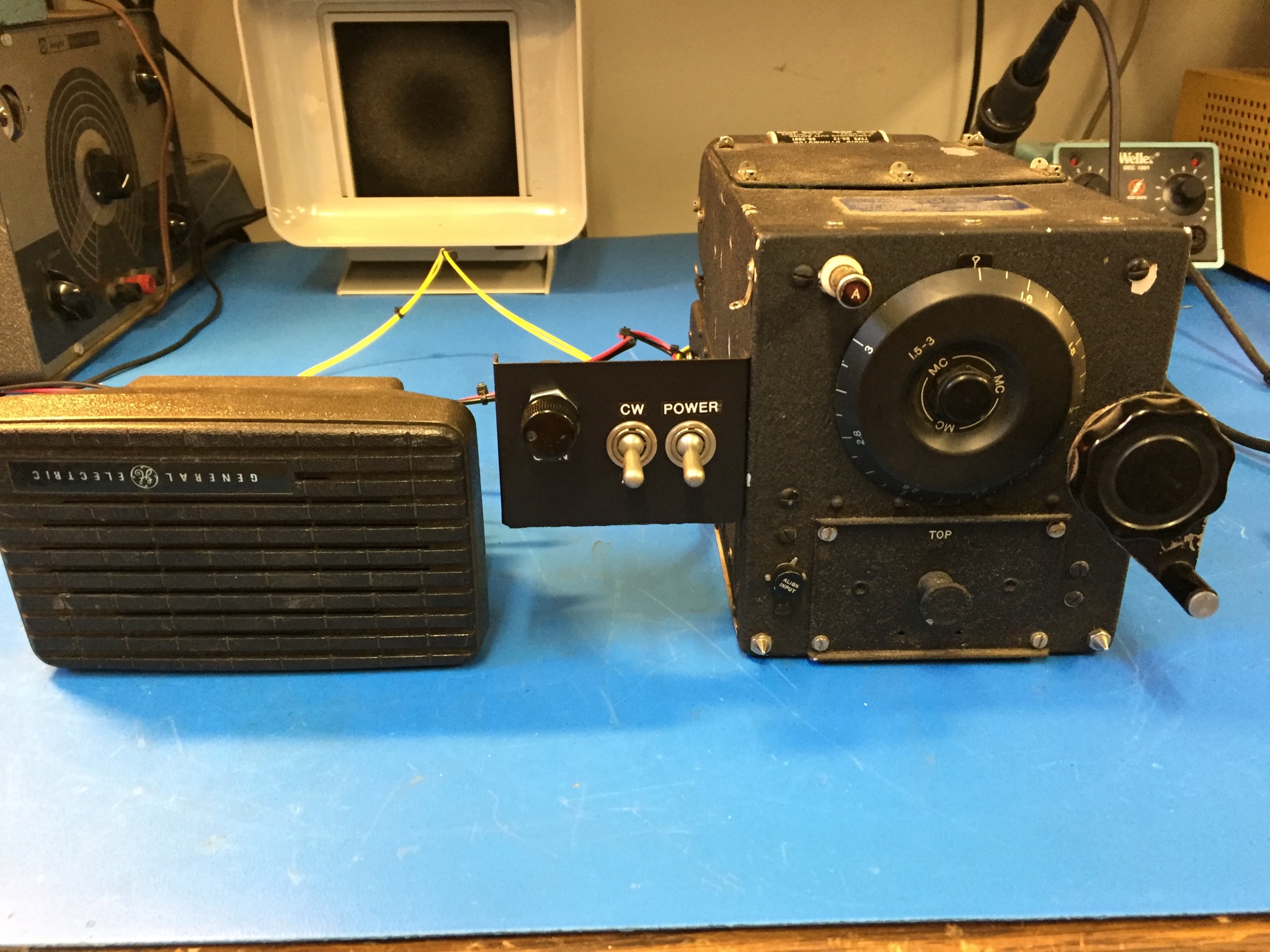
Now that everything was in order it was time to try the radio in its final configuration. I connected up my 20 m external dipole and powered up the radio. The whrrrr was smoother than ever. Within seconds stations starting coming in strong, much louder than before. I tweaked the antenna coupling control, they were louder still. I listened to a basketball game from an AM broadcast station in Chicago, I tuned into WWV at 2.5 MHz, and tuned in an 80 m AM net. What an incredible receiver, it was wide awake and operating to its original specifications once more!
AFTER 3 YEARS OF OPERATION…
This unit switches-on every time without fail, whrring away for innumerable demos for friends and family. Everyone is thrilled and amazed to see a dynamotor-powered receiver that is running almost entirely on its original parts and as it was originally built.
By accident I even connected the DC input backwards, reverse polarity. The dynamotor roared into life but the radio never produced audio. I figured out the problem after about five minutes of reverse polarity operation. Fortunately for me, and unlike solid state equipment, no damage was done. I re-connected it the correct way and it worked just as well as it did before.
IF IT’S FROM WW2, DON’T HACK IT, PRESERVE IT!
We are now at a point where the surplus WW2 electronics should no longer be hacked to bits. Join the movement, there are many others who restore WW2 and other vintage gear to be original as possible. Most of the community orbits around Electric Radio Magazine. Test those capacitors before throwing them in the garbage and keep those filaments lit!
No comments:
Post a Comment